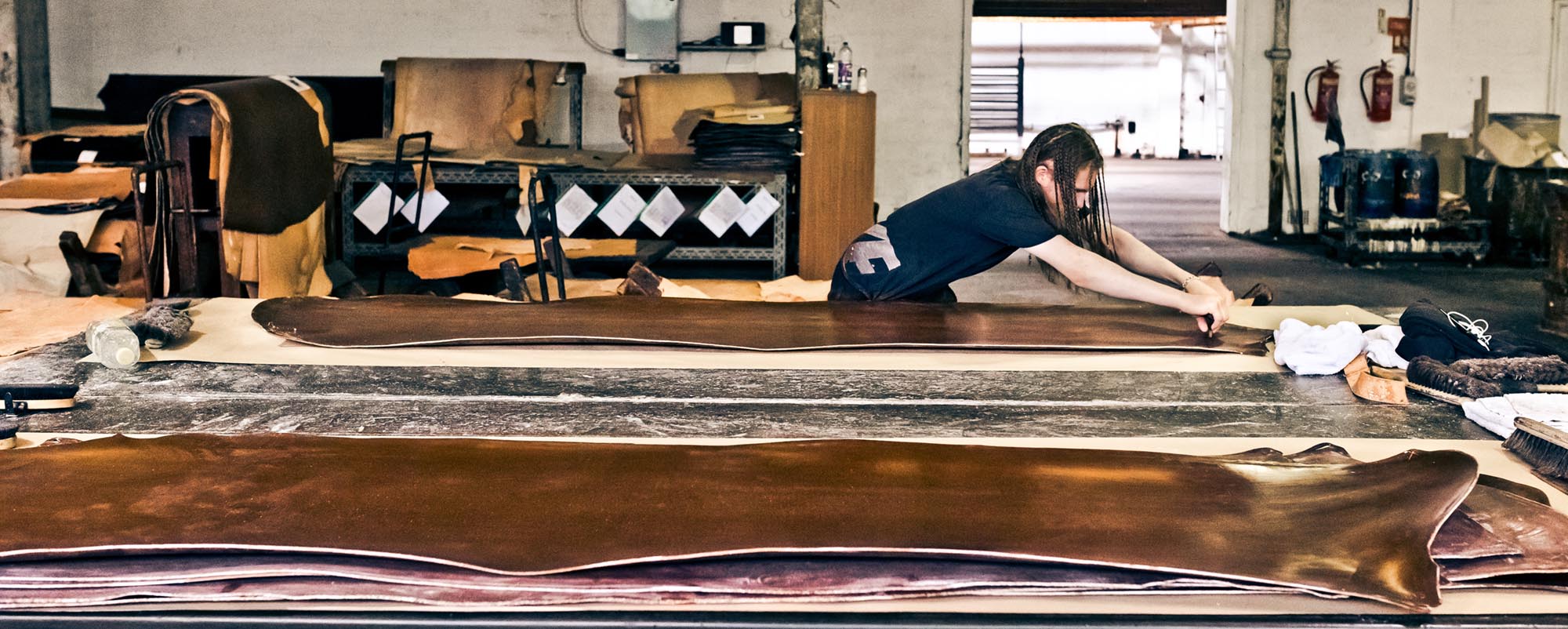
Words by Jonathan Foyle
Photography by Paul Read
Among the associated trades of leatherwork, the purpose and value of the currier tends to be forgotten. These artisans command an array of traditional hand-worked leather treatments from which we all benefit. They receive hides from a tannery and then sort them, shave them to required substance, drum and samm/set them, then handset and dry the leather before finishing it through a process of buffing, colouring, printing and greasing. This gives the leather a high shine finish that protects it for its future use by the equestrian and leather goods manufacturing trade. Hand currying is crucial to the quality of the finest leatherwork. The problem is not just that the contribution of curriers tends to be overlooked, but that their trade has largely disappeared, their skills lost to automation.
Walsall in the West Midlands was the heart of English leatherworking. In the Middle Ages loriners (makers of small metal parts for horse apparel) used Walsall’s local coal and ore to forge metalwork for the town’s saddle makers. By the 19th century the town provided equestrian leather goods for the British Empire, the proceeds from which funded its Victorian urban core. Marsh Street hosted D Mason & Sons Universal Leather Works, incorporating the family’s currying workshop, one of many. That firm is long gone, though the handsome red brick factory still stands. Much of Walsall’s leather industry has disappeared completely. A museum of 2,000 objects remains to account for it, as if the Mary Rose had sunk here.
But there is a living legacy amongst the town’s curriers and finishers. “I knew there was leatherwork happening in Walsall”, says local 19-year-old Jack Rushton, who was on Universal Credit into the summer of 2021, “but I thought it was making saddles, or something. There was more involved than I thought.”
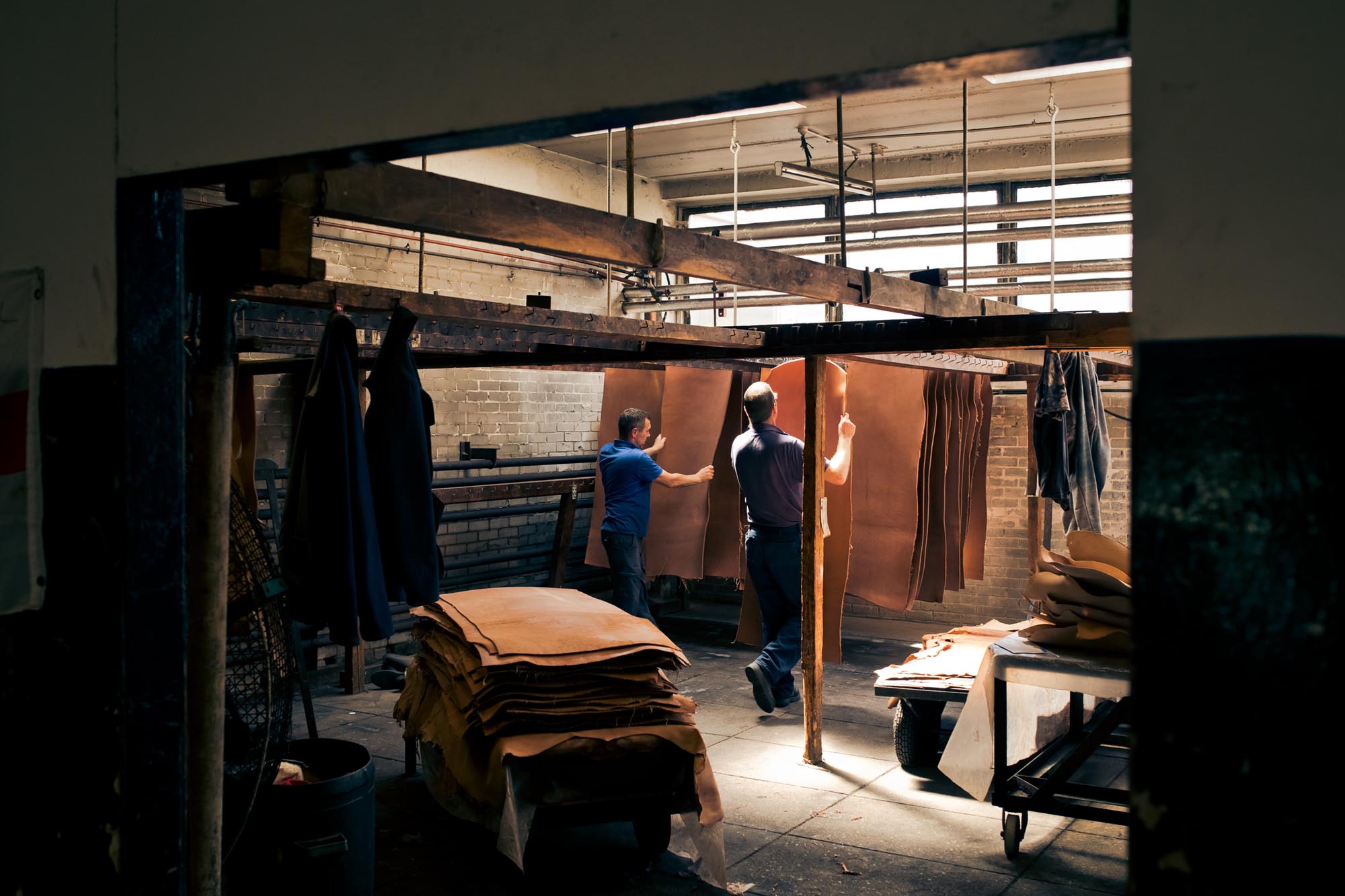
Jack is one of three apprentices who have come to work at J & E Sedgwick, Walsall’s last curriers and finishing factory. It’s an old company, founded in 1900 and established in this building in 1956. The Clayton Leather Group, which owned Sedgwick’s, faced administrators in 2018, but while their other workshops saw unsustainable losses, Sedgwick’s books recorded a regular profit so the factory was saved from liquidation.
The current General Manager, Philip Bevington, has serviced that demand both before and after the UK’s decision to leave the EU. The long-standing markets for the best British leather remain in Japan and India, where the best bridles are prized. Yet the workforce is ageing, and future orders may have too little labour to service them.
“Currying is hard work, treating a thick piece of leather the size of a desk. And they were all older guys when I arrived, in their 40s, and 50s”, he explains. “We have a problem attracting young people.” He muses that school leavers are usually directed toward a college or university education, and don’t expect the manual labour of factory work, hauling and pushing and stretching heavy hides. If artisanal trades are hands-on heritage, with the finesse and creativity of cooking, then prospective talent needs a pipeline of young people to learn on the job.
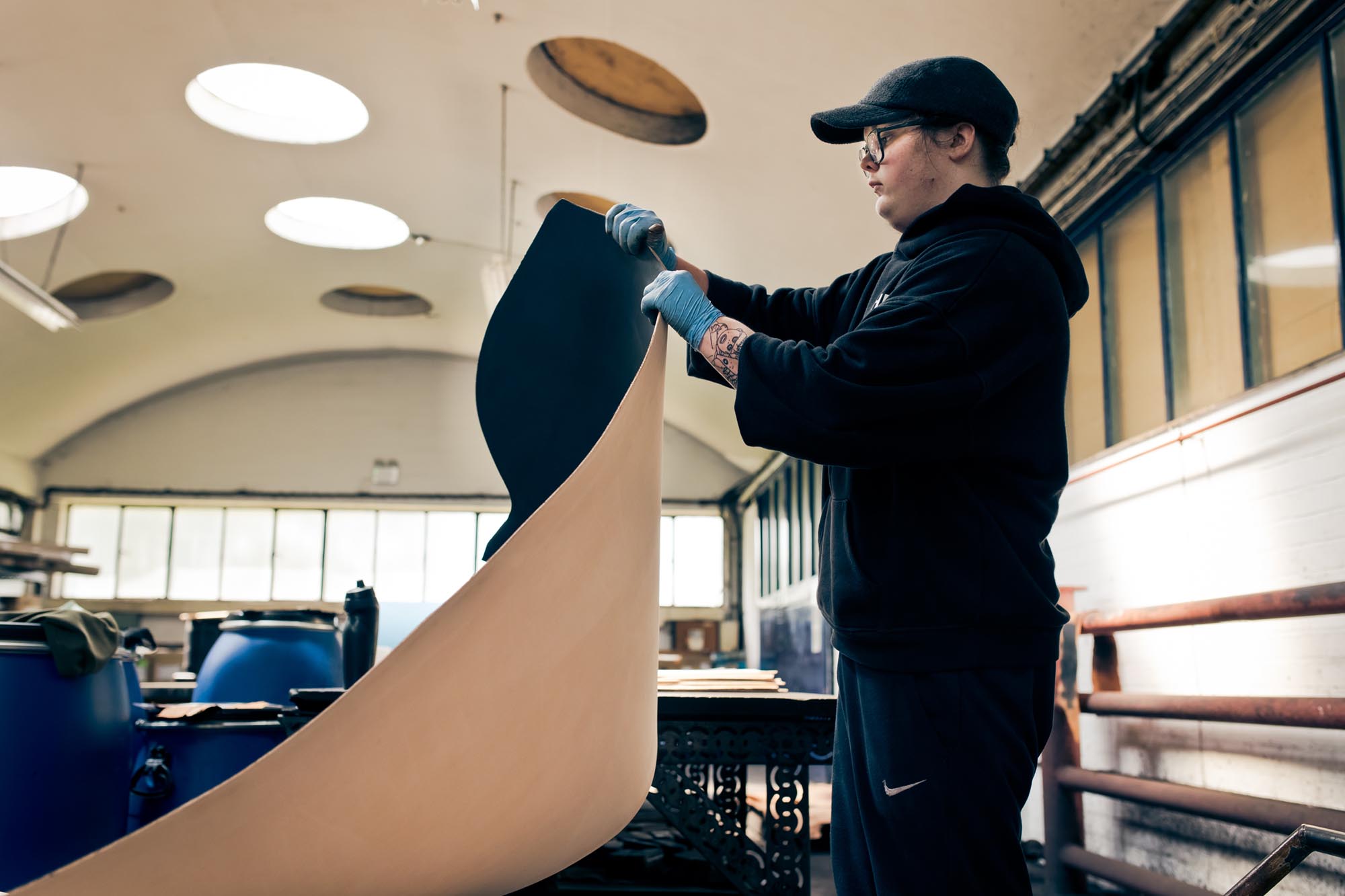
“Once-strange machinery is now familiar. And he has a new way of thinking about his work. If you make it by hand, you make it with pride. It’s always got your stamp on it.”

The Kickstart Scheme was brought in by the government to offer funding support for new jobs aimed at 16–24-year-olds at risk of remaining on Universal Credit. Philip Bevington approached Walsall Council about it. The main problem was assessing applicants’ suitability to be trained for hard and detailed work, so an honest introduction was essential. Walsall College once offered courses in leatherwork, generating skilled graduates. Now, he says, “the best way to gauge whether someone will stay the course is through an interview that includes time on the factory floor.”
The approach has succeeded. “I’d never done any work like this before”, says Kameron Tranter, 24. Kameron’s interests lay in creative arts, music mixing and sound production, but his previous jobs were temporary. For much of his youth he had moved around, between care homes and foster families in the Birmingham area and described teachers as “confidence-knocking”. But he is now settled into this job, as “it’s given me a lot of structure” and offers a variety of tasks that avoid monotonous routine. Once-strange machinery is now familiar. And he has a new way of thinking about his work. “If you make it by hand, you make it with pride. It’s always got your stamp on it.”
Lucy Burbridge is 21. She’s a natural maker with an eye for intricate detail, evidenced from her time working in stage and prop design. She recalls that “I signed up for Universal Credit, and my work coach sent the link to the Kickstart schemes. I really enjoy making the spray dye colours, which requires judgment and adjusting. There’s a physical aspect to it too, all day picking up, pinching, hanging, handling.” Jack was less professionally focused: “I was open to anything, really.” His brothers worked in car parts, his mother and sister in care. He describes the cycle of currying, where 400–500 hides usually arrive at the start of a calendar month and take several weeks to process. The part Jack enjoys is ‘pebbling’, which leaves a high-shine greased finish to the surface. But he found a particular satisfaction in the handbrushed staining of the skins. That engagement has meant Jack is 10 months in and counting.
The Kickstart scheme is now finished, but it has brought young people into the currying and finishing trade from varied walks of life. Each is making a distinctive contribution while gaining a satisfying sense of purpose. The challenge now is to build on that success and use these stories for more young people to reimagine a future based on the fundamental qualities of handmaking skills.
As part of our commitment to supporting the UK leather trade we are proud to have launched two new grant programmes in 2022, offering £5,000–£10,000 to tanneries and established artisan makers to take on apprentices and pass on essential skills to the next generation.
READ MORE
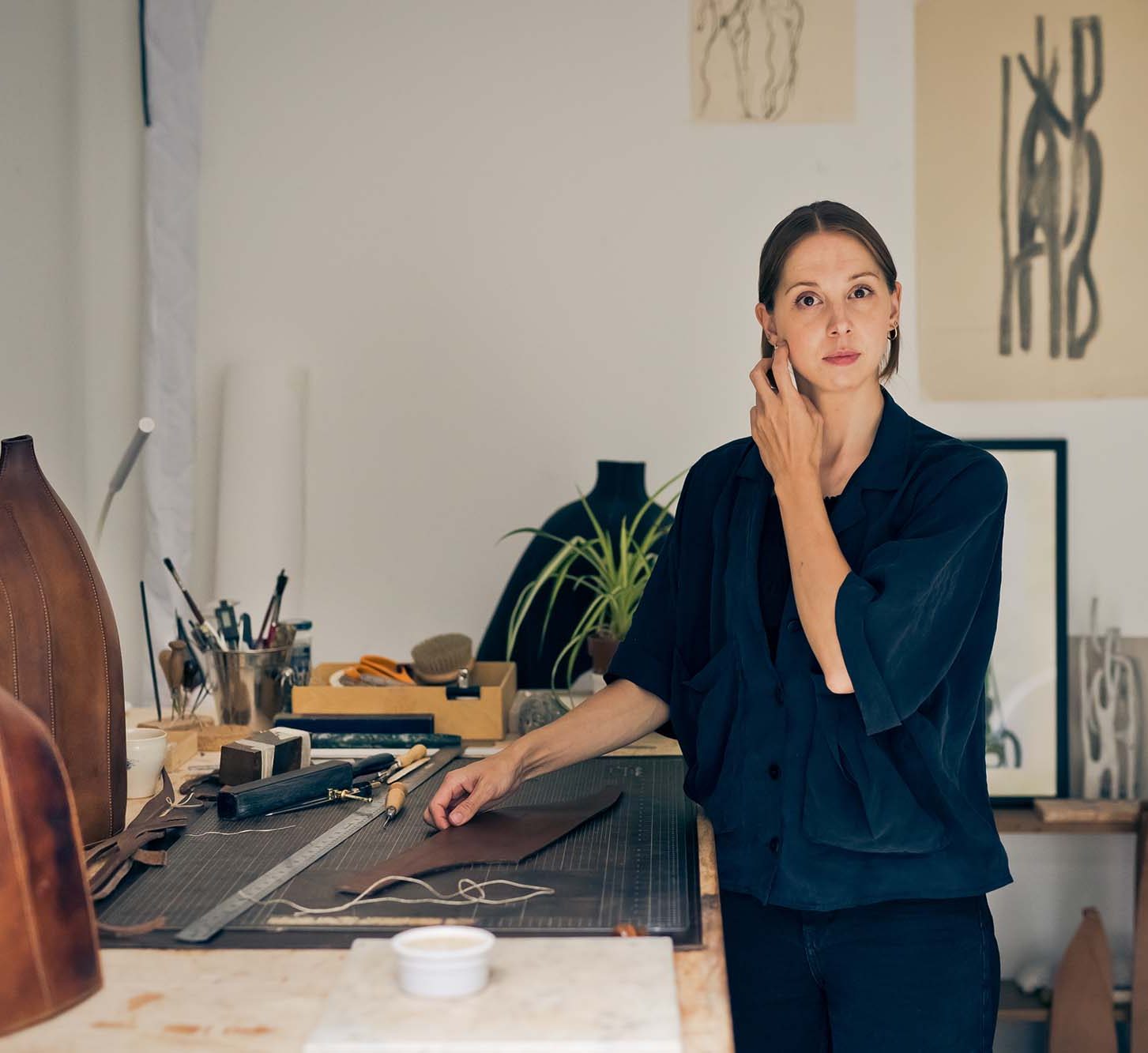
Dream Maker
In her sleep, Frances Pinnock finds inspiration for her figurative leather sculptures.
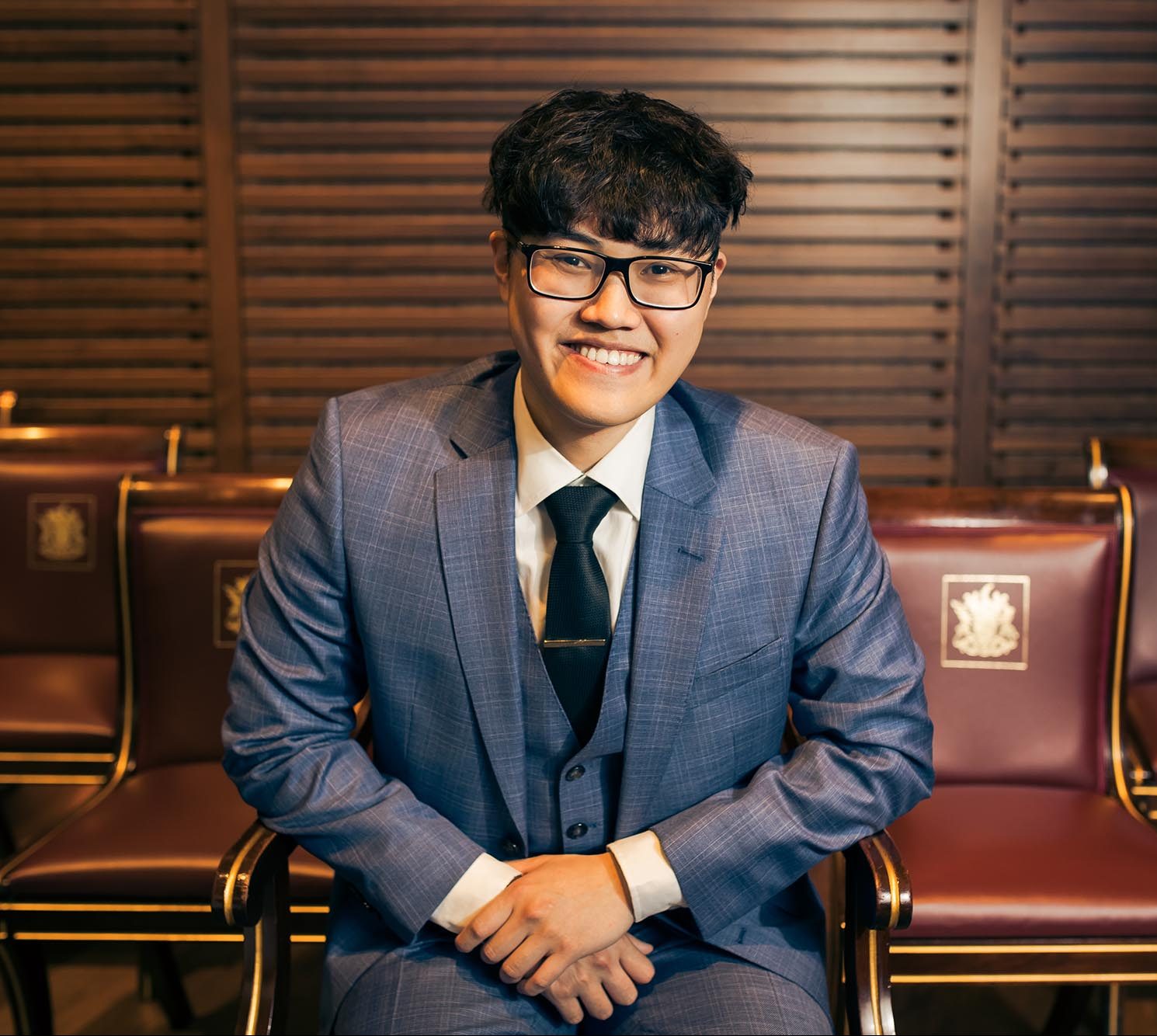
Life-Changing
Celebrating the long-term success of the Leathersellers’ Scholarships at Colfe’s School.
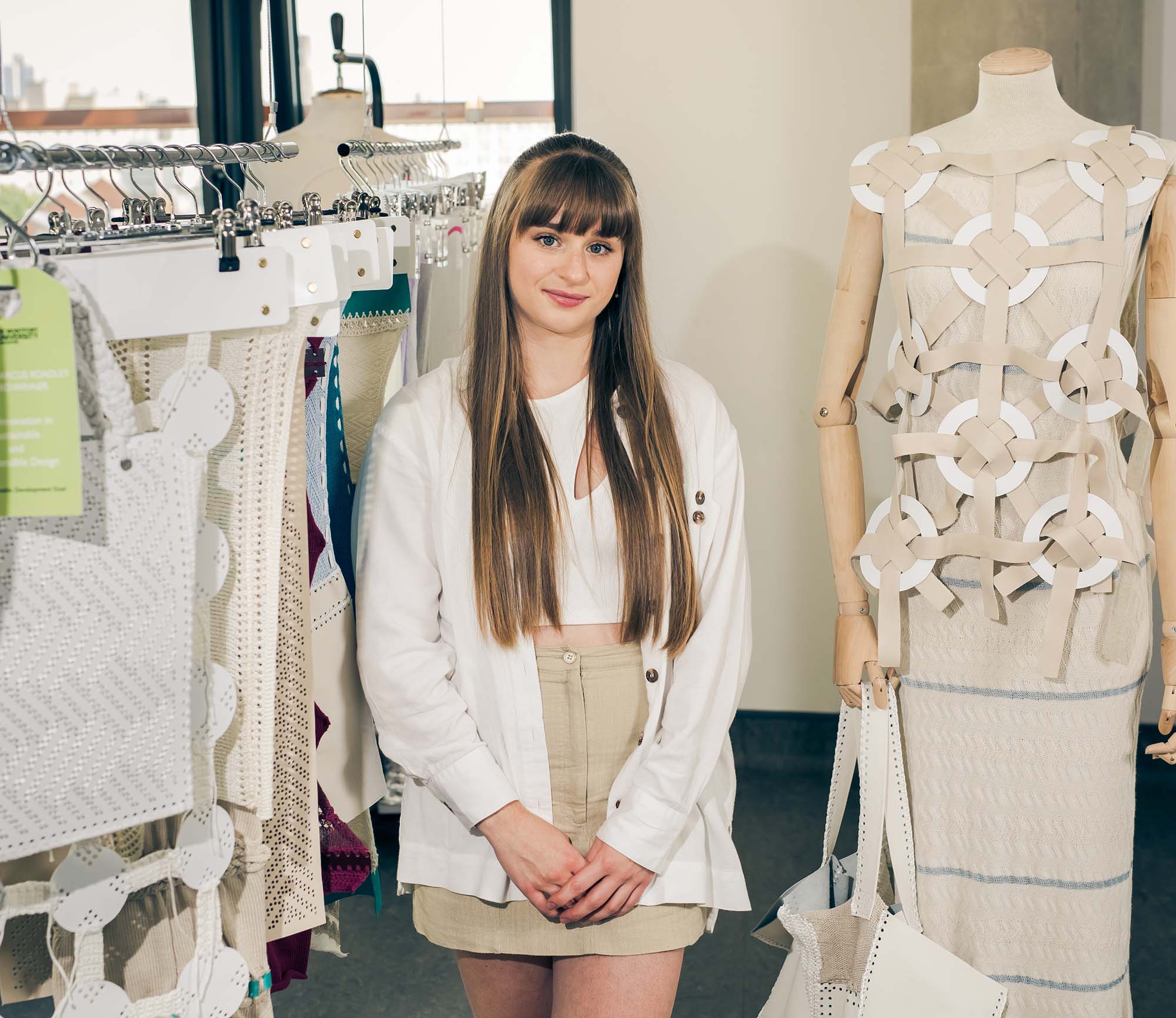
Fashioning History
For an inspired project at Leicester’s De Montfort University, students of “Artifacts Live” are drawing on the lessons of historic leathercraft to create the designs of the future.